Preparation of powder
Alumina powder is prepared into powder material according to different product requirements and different molding process. The particle size of powder is less than 1μm. If it is necessary to manufacture high purity alumina ceramic products, in addition to the purity of alumina should be controlled in 99.99%, it also needs to carry out ultrafine grinding process to make its particle size distribution uniform.
When using extrusion molding or injection molding, binder and plastic agent should be introduced into the powder, generally in the weight ratio of 10-30% thermoplastic plastic or resin, organic binder should be mixed with alumina powder at 150-200℃ temperature evenly, in order to facilitate the molding operation.
The powder materials formed by hot pressing process do not need to add binder. If the use of semi-automatic or automatic dry pressing molding, there are special technical requirements for the powder, we need to use spray granulation method to treat the powder, make it appear spherical, in order to improve the fluidity of the powder, easy to fill the mold wall automatically in the forming. Spray granulation of powder is required during dry pressing, and polyvinyl alcohol is introduced as binder. In recent years, a research institute in Shanghai has developed a water-soluble paraffin as a binder for spray granulation of Al2O3, which has good fluidity under heating. The powder after spray granulation must have good fluidity, loose density, flow Angle friction temperature less than 30℃, ideal particle size ratio and other conditions, so as to obtain a higher density of plain green.
Molding method
The molding methods of alumina ceramic products include dry pressing, grouting, extrusion, cold isostatic pressing, injection, flow casting, hot pressing and hot isostatic pressing. In recent years at home and abroad also developed pressure filter molding, direct solidification injection molding, gel injection molding, centrifugal injection molding and solid free molding molding technology methods. Different shapes, sizes, complex shapes and precision of products require different molding methods.
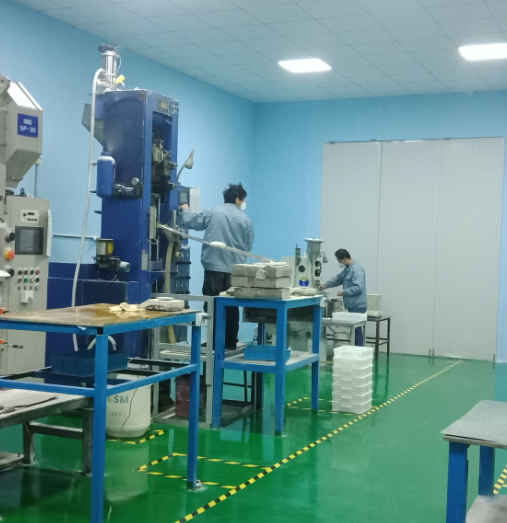
Post time: May-09-2022